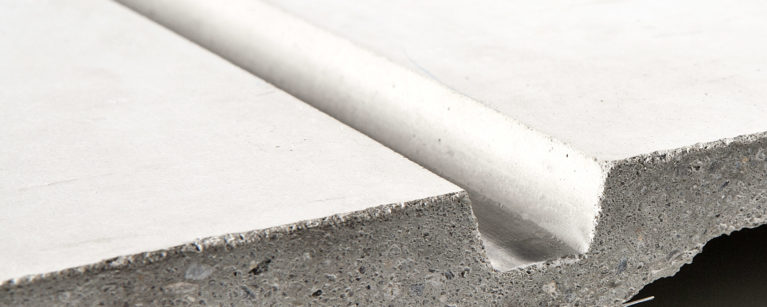
Composite materials are on a strong upsurge as demands in the construction industry rise up. Wood and plastic are pressed and moulded together in compression. Steel rebars are embedded in a concrete matrix to form a rigid reinforced material. As technology advances, so does the building material.
A strengthened material is composed of a matrix and reinforcement. Conventionally, reinforced concrete is only limited to the tensile strength of steel. Today, glass fibre reinforced concrete (GFRC o simply GRC) is mounting towards success as it effectively replaces steel with glass fibres. These high-strength glass fibres are imbued in a concrete matrix of fine sand, cement, admixtures, polymer and water.
These elements thrive together and form a synergistic compound than when specified alone. Concrete alone would be prone to cracking. The glass fibres exude the flexural and tensile strength needed by the compressive concrete. As these glass fibres carry the tensile loads, the concrete matrix acts as a medium to bind and transfer the loads.
Initial glass fibres lack durability since the alkaline cement reacts with silica. Since the 1970s, a 19% of zirconia is added into the content to render alkali-resistant (AR) glass fibres. Furthermore, GRC is continuously commercialised due to its high damping capability, low rate of thermal expansion, waterproofing and corrosion resistance.
While GRC panels look similar to the prefabricated concrete panels, they differ intrinsically in their properties. GRC achieves the pseudo effect through its reduced thickness; they are 80% lighter than precast panels. The superimposition of loads on the building frame is lessened. Thus, GRC panels pose as an economical, lightweight and impact-resistant alternative.
Complex geometries of parametric designs and heavy ornamentation can be achieved easily through GRC. The design process of GRC façade elements typically starts in a pre-programmed 3D modelling software and then manufactured in a factory with controlled systems. Through the use of computer numerical control technology (CNC), intricate reusable moulds that require tight fabrication tolerances can be pre-produced, while laser cutting can be employed after casting.
Premix
Treated as the simplest technique, premix method makes use of the conventional concrete mixer to blend short fibres and concrete slurry. The premixed GRC batch can be sprayed, troweled or placed into a mould for vibration. Compaction may decrease the strength of GRC so these fibres are added at the final stage of mixing cycle to reduce damage. Premix method naturally results in lesser strength levels due to the decreased concentration and random orientation of short glass fibres.
Spray-up
This direct-spray method is similar to the application of shotcrete. The concrete mixture is sprayed from a cement-sand slurry gun onto a pan, while glass fibre chopper simultaneously cuts long fibre strands from a continuous spool. This method produces a stronger, two-dimensional fibre orientation as compared to the premix method.
GRC’s multiple applications range from sandwich panels, decorative trims, accent features, countertops and architectural facade claddings. It can also be finished with integral pigments, stains, coatings and textures.
However, its installation is not only limited to modern design. Structural and plumbing systems, such as retaining walls and sewer pipes respectively, also utilise this all-in-one building material.